Dry powder Mixing process problem and challenge
input time:2022-03-02 09:43:07 hits:
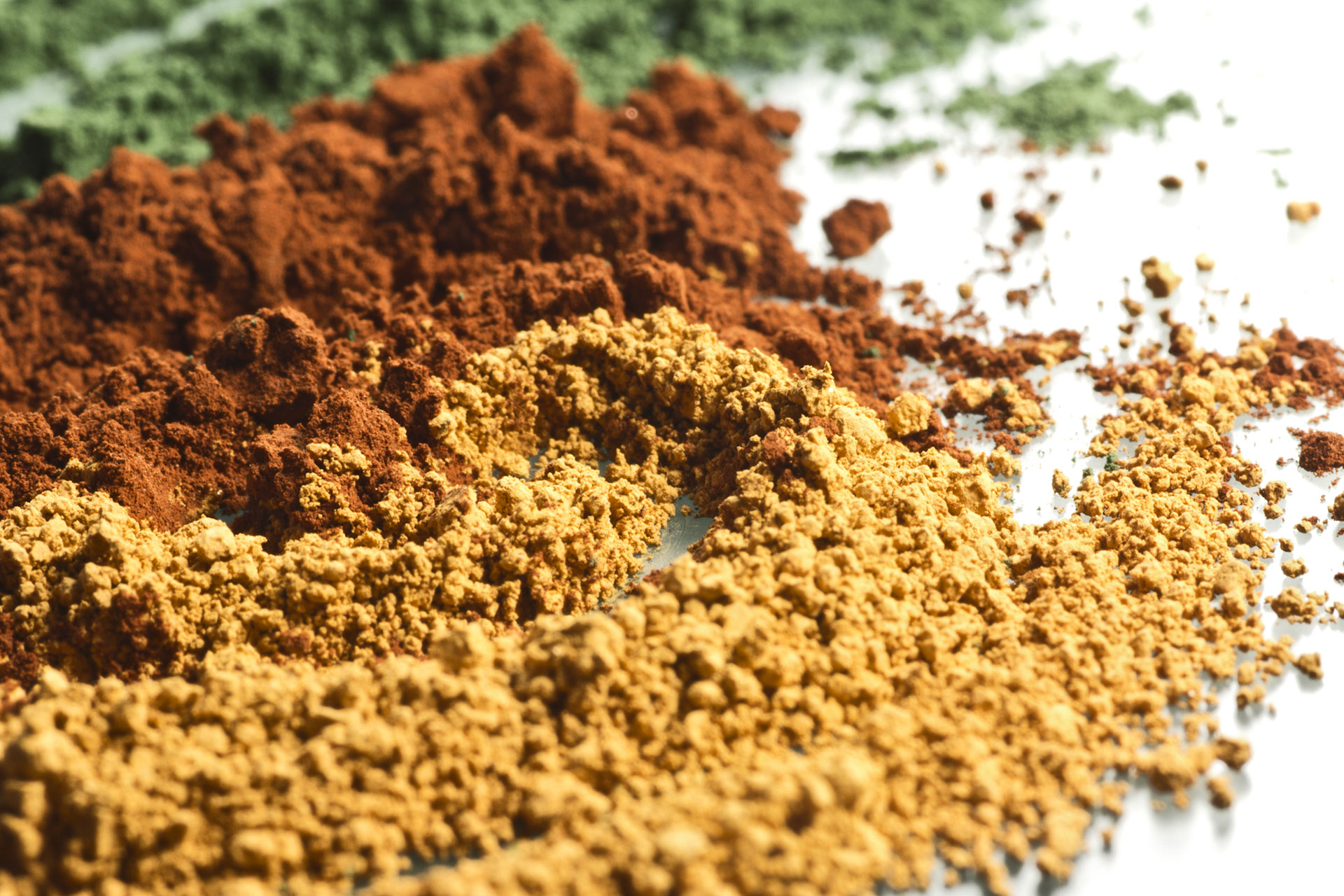
The traditional mixing challenges and solutions:
1. powders with super light weight can not be mixed with the main mixing batch
this is a classical mixing challenge. for example, in the case of adding 0.5% carbon powder to iron powder, the specific gravity of which is 10 times bigger than that of the carbon powder, the method of pretreatment can not slove the problem of this discrepancy due to the characteristics of the mixing materials.
when using the 3D mixer to mix, carbon powders will keep flow on the upside of the container vessel and unable to be mixed in with the mixing batch because of the light weight. extending the mixing time is not going to work as well. this mixing challenge will be present when the gap of the specific gravity of the light-weight powder and the main mixing powder is over 100%.
such being the case, the problem can be solved by using double movement mixers.
Because of the larger loading capacity of the double movement mixers, there is little room left in the container for the light-weight powder to flow. in addition, since full-size blades inside the vessel have the capability of mixing the light-weight powders into the main mixing batch, this problem is solved effectively.
2. powders with low volume are difficult to be blended in.
when powders are refined to certain extent, the physical characteristics of the powders will have fundamental alterations and its motion activity will have a big increase.
in case of silica sand with big specific gravity, its particle can flow in the air when its particle diameter is equal or less than 10 micrometer. the powder with more than 3000 mesh number is even more active, because the smaller diameter and lighte weight allow it to have the capacity of flow,absorption and aggregation.
it is very difficult to mix powders with diameter less than 1000 mesh numbers.
super low volume powders with the capacities of flow, absorption and aggregation will float just like the powders with super light weight, so it is a tough task to blend them in.
adopting the double movement mixers can slove this difficult due to the fact that the rotation of the container and the blades can push the light-volume powders to the mixed with the main mixing batch and the shear force of the inside blades can prevent and break the lump and aggregation.
3. the influence of flowability over the mixing process
generally speaking, the better the flowability of the powder is, the easlier the mixing will be. the flowability can be tested by piling up the powder along the wall. the samll angle means the smooth of the powder and a good flowability. the flowability is bad with the angle over 40 degrees. powders with angle over 45 degrees will be very difficult to be throughly mixed by traditional 3D mixers. so, when mixing powders with large stickness, some users install the steelchains and steelballs inside the vessel, the movement of throw and swing of which will exert shear and grind force over the powder. even though the mixing problem can be solved this way, the collision and grinding between the steelchain and the vessel create impurity contamination. therefore, we need to choose mixers with shear and agitation forces to have this problem solved.
4. the influence of fake particles over the effect of the mixing
fake particles refer to the granule caused by the aggregation of small particles. there are various reasons for the formation like: dump plate, absorption of static electricity,and stickness caused by the high working temperature. in the course of powder mixing, fake particles will affect the mixing effect and the quality of the final product if not be break down. shear force to break the stickness of the small powders is necessary for the uniform blending. Therefore, the mixer with inside blades to cut,break down fake particles will be of better mixing effect. If the stickness between the powders are too strong and too solid, double movement mixers can not break the lumps completely and it will need additional help from other equipments.
5. dynamic segregation after the mixing process
For these kinds of powders with good flowability and big weight discrepance, even though they are uniformly mixed,transportation process can lead to the dynamic segregation of light powders on the top and heavy powders at the bottom, which will create difficulties for the further manufacturing processes, resulting in poor product quality. Therefore, it is necessary to adopt compact packing or vacumme packing to avoid dynamic segragation.
6. various technical problems present in the actual mixing process
some of the problems are beyond the scope of this article and we welcome peers from all industries to contact us and work together to solve the mixing problems.