Dual motion mixing equipment has excellent application in refractory industry. Alkaline refractories are mainly composed of magnesium oxide and calcium oxide. magnesium brick containing 80%~ more than 85% of magnesium oxide has good resistance to alkaline slag and iron slag, and the fire resistance is higher than that of clay brick and silicon brick. Mainly used in open furnace, oxygen transfer furnace, electric furnace, non-ferrous metal smelting equipment and some high-temperature equipment.
Refractories used in special occasions include high temperature oxide materials, such as alumina, lanthanum oxide, beryllium oxide, calcium oxide, zirconia, etc., refractory compound materials, such as carbides, nitrides, borides, silicides and sulfides. These materials generally require high mixing uniformity, but the advanced application of double motion mixing equipment in the equipment industry can fully meet the needs of the industry and improve the high quality and high yield products for the refractory industry.
The high temperature composite material in refractory mixing is the most common, and it also has certain requirements for mixing equipment in process production. It mainly includes cermet, high temperature inorganic coating and fiber reinforced ceramic. Commonly used refractories are AZS brick, corundum brick, directly combined magnesium chromium brick, silicon carbide brick, silicon nitride combined silicon carbide brick, nitride, silicides, sulfides, borides, carbides and other non-oxide refractories; calcium oxide, chromium oxide, alumina, magnesium oxide, beryllium oxide and other refractories.
Often used thermal insulation refractories are diatomite products, asbestos products, insulation panels and so on. The commonly used amorphous refractories include supplementary charge, tamping material, castable, plastic, refractory mud, refractory spray material, refractory castable, refractory coating, light refractory castable, gun mud and so on.
During the production of refractories, mixing equipment and its advanced mixing process are very important links; because uniformity directly affects the various properties of the product, such as porosity, bulk density, water absorption, permeability, pore size distribution, thermal shock resistance, slag resistance, acid resistance, alkali resistance, water resistance, CO erosion resistance, electrical conductivity, oxidation resistance, etc. As a result, the uniformity of mixing materials is a very important indicator. The traditional mixer is a kind of gravity diffusivity mixer (3D mixer, V mixer, double cone mixer, etc.): low efficiency, high energy consumption, low equipment utilization and low uniformity; another kind of forced shear mixer (horizontal screw belt mixer, single cone mixer, etc.); the material mixing dead angle exists in the cylinder, it is easy to destroy the particle size or properties of the powder itself, so it can not be refined and uniform. There is also a kind of innovative dual-motion mixer which combines the advantages of the above traditional mixer. When the cylinder rotates, there are full-size spiral blades in the material for multi-directional shearing, holding and stirring.
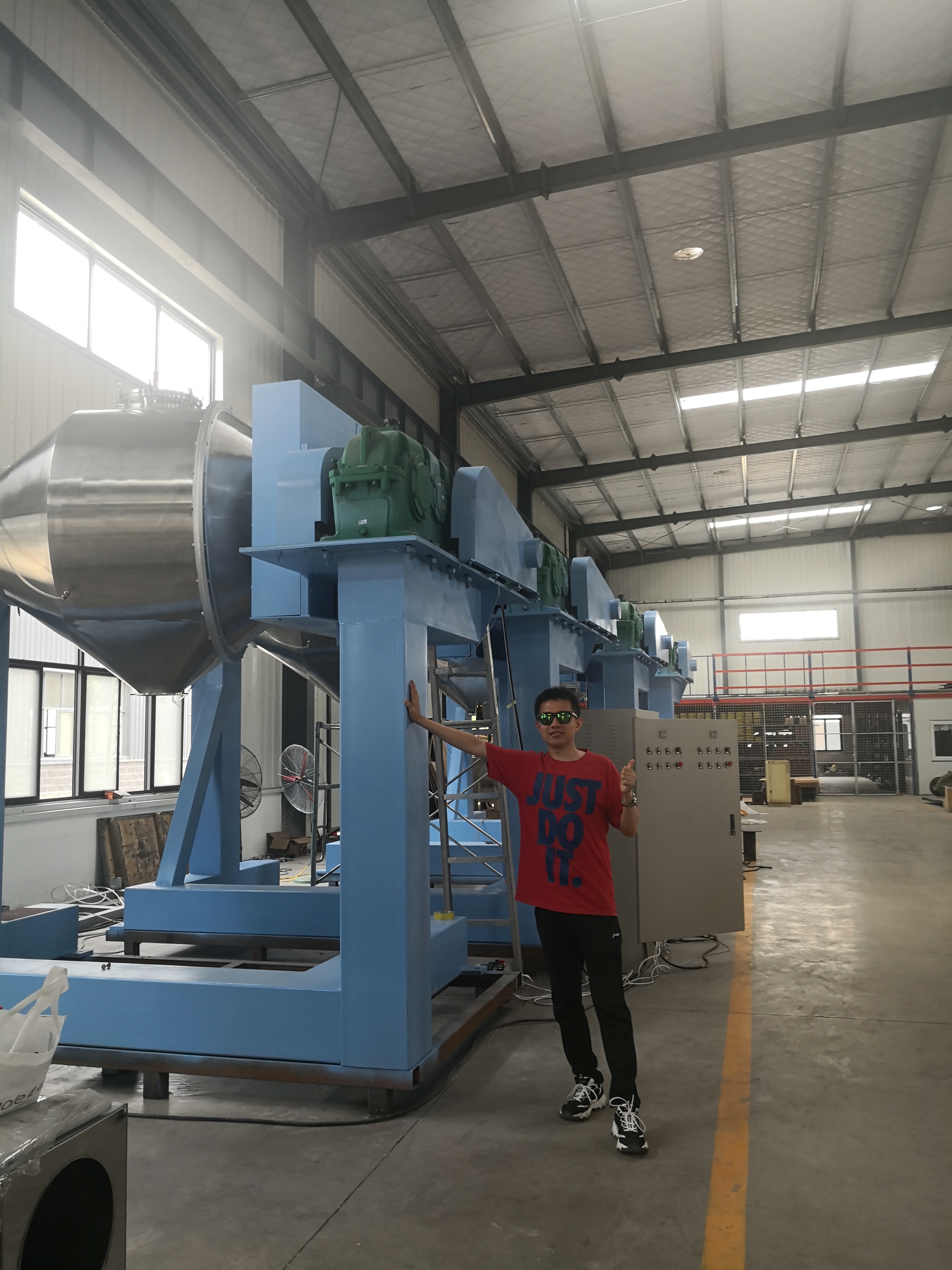